The metal fabrication industry is an integral part of the global economy, serving as the backbone for various sectors including construction, automotive, aerospace, and consumer goods. This industry transforms raw metal materials into finished products through processes like cutting, bending, welding, and assembling. Globally it is valued at over 20 billion in 2022 and poised to grow to over 31 billion by 2031!
Metal Fabrication Explained
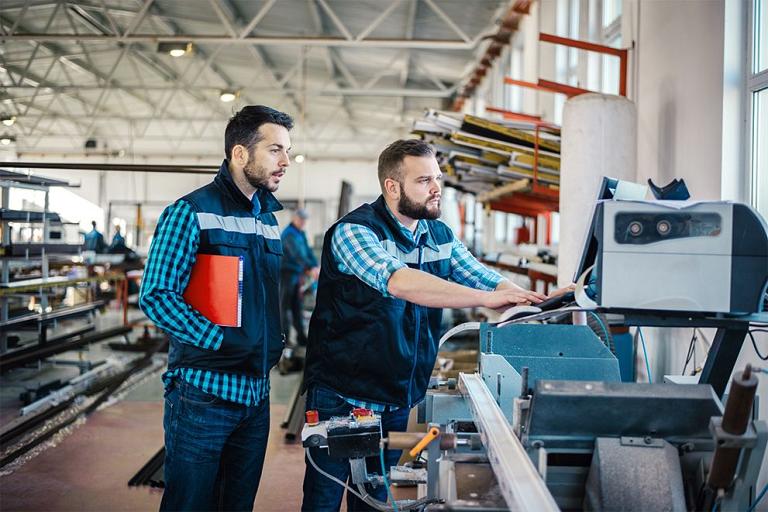
From its beginnings in ancient civilizations, where early metalworkers created tools, weapons, and structures from basic metals, through the Industrial Revolution, which saw the advent of machinery enabling mass production and large-scale industrial applications, to its current status as a highly sophisticated and technologically advanced sector, metal fabrication has come a long way. Today, it encompasses a vast array of activities, from producing small components to constructing large structural frameworks for buildings and infrastructure.
Metal fabrication is a manufacturing process used to shape metal into parts or end products. It usually consist of three phases: 1) design, where shop drawings are created to the intended measurements; 2) fabrication, which involves cutting, bending, and/or assembling; and, 3) installation, where the end product or structure is put together (either partially or fully). Most metal fabrication uses sheet metal, which can be up to 0.25 inches thick. Fabricators convert this sheet metal into products or tools that get stamped, folded, shaped or joined to create a finished component.
What Industries Use Metal Fabrication?
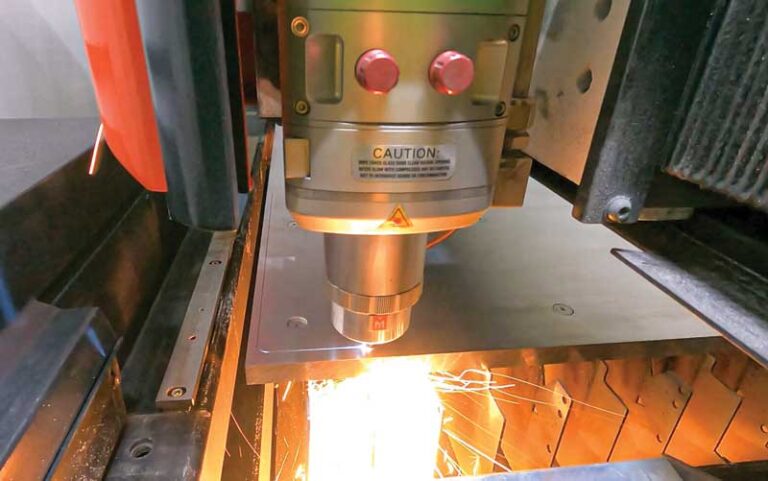
Metal fabrication has applications in a wide variety of industries. Because of the versatility of tools and processes, it’s used to create parts for industries as varied as agriculture, spas, military craft and cars. Three of the most common types of metal fabrication include structural, commercial and industrial.
Structural
Structural fabrication refers to metalworking done as part of the building process. The construction industry is one of the largest consumers of fabricated metal products. Structural steel and metal components are essential for building skyscrapers, bridges, and other infrastructure projects. In a commercial setting, the steel is likely what helps form the foundation. Think — New York City’s Empire State Building, the Sydney Harbour Bridge, and Dubai’s Burj Khalifa, the world’s tallest building — all constructed with structural steel.
High-strength structural metal is one of the most popular materials used in the construction field today, whether the project is commercial, industrial, or residential in nature. The types of metal parts that may be used for a structural project including towers, or custom-made parts of a facility that enable more enhanced production, platforms, which often form a part of loading bays, storage locations, ramps, or decks in certain facilities, walkways, stairs, and structural components that make up the main framework of a particular building (e.g., trusses, girders, and beams).
Commercial
Commercial fabrication involves creating products for consumer use in sectors like automotive and appliances, where metal fabrication is crucial for making vehicle frames and engine components using advanced techniques for lightweight, durable materials essential for fuel efficiency. It also includes components for restaurants, stores, public spaces, and municipal buildings, such as guardrails, awnings, shelving, sinks, and conveyors, which tend to be smaller and require higher precision compared to structural and industrial metal parts.
Industrial
Industrial fabrication produces large-scale pieces for equipment used in manufacturing consumer goods, serving industries such as aerospace, material handling, pollution engineering, water treatment, alternative energy, and automotive. Products created through industrial fabrication include ironworking machines, bandsaws, tanks, silos, and heavy machine parts. In the aerospace industry, for instance, metal fabrication is crucial for manufacturing aircraft components that meet high safety and performance standards due to its precision and durability.
Types of Metal Fabrication Processes
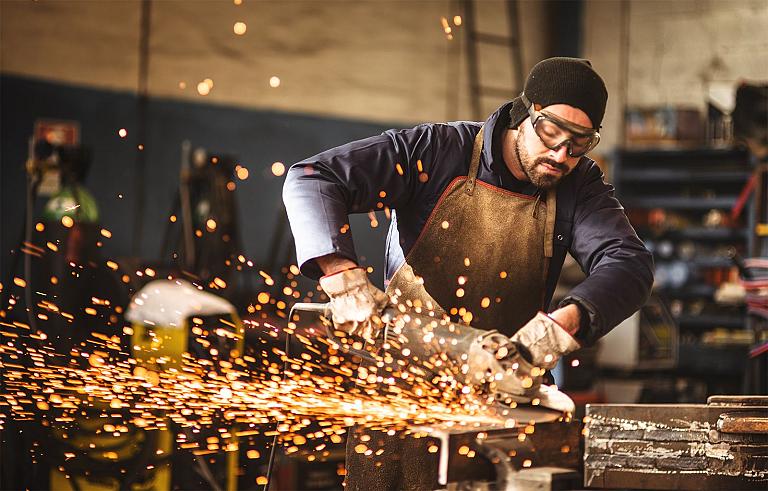
Cutting
Laser cutting: A technique that uses high-intensity light beams to cut metal via burning, melting or vaporizing.
Saw cutting: A highly precise cutting method requiring skilled workers and specialized saw blades.
Bending
Bending and forming: The use of hydraulic equipment, CAD/CAM capabilities and various tools to bend and shape materials to fit specifications.
Welding
A fundamental process for joining metal pieces, which can involve various techniques such as:
- Robotic Welding: Automated welding for consistent and efficient joints.
- TIG (Tungsten Inert Gas) Welding: Known for its precision and strong welds, commonly used for thinner materials.
- MIG (Metal Inert Gas) Welding: Popular for its speed and versatility, suitable for a wide range of metals and thicknesses.
Finishing
Grinding and Polishing: These processes ensure a smooth and consistent surface for metal products with tight tolerances.
Powder Coating: An alternative to traditional painting, this process applies a durable and custom coating to metal parts.
Machining
CNC Machining: A method of fabrication for prototyping and high-volume production that utilizes programmable computer software for ultimate precision and efficiency.
Assembling
Assembling: Involves putting together different metal components to form a final product, often including fasteners, adhesives, or other joining methods.
Metal Fabrication Advancements
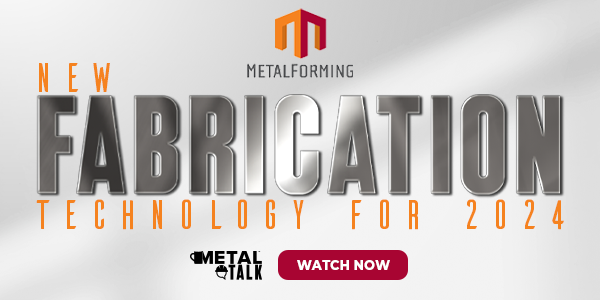
Thanks to our good friends at MetalTalk, this podcast takes a deep dive into the new fabrication technologies for 2024. Hosted by co-founder Karen Edwards, the episode features discussions with Chad Rowe, Ken McLauchlan, and Stephen Gosk with MetalForming, one of METALCON’s exhibitors. Watch it ➡️➡️ here.
They highlight several innovative technologies aimed at meeting the growing market demands and improving the efficiency and capabilities of metal fabrication processes, including:
- Board & Batten Design: Technology that enhances the aesthetic and functional aspects of metal panels, making them more versatile for various construction applications.
- Conical Bending: While this method isn’t new, to meet the needs of complex architectural designs, the machinery can now put the exact parameters into a CNC system to lay it out, allowing for more precise and efficient bending of metal sheets into conical shapes.
- Profile Manipulator Technology: This technology facilitates the manipulation of metal profiles to create custom shapes and designs, improving flexibility and creativity in metal construction.
For additional resources on metal fabrication, contact one of METALCON’s industry partner associations — Fabricators and Manufacturers Association (FMA) – the leading organization that advocates for the growth and advancement of the metal forming, fabricating, and manufacturing industries through education, networking, and innovation..
Learn More About Metal Fabrication with METALCON
There is no better place than at METALCON to learn more about metal fabrication. From the exhibit hall to in-depth workshops, the opportunity to network and learn from industry experts is endless. Check out the exhibitor list and floor plan where you’ll find dozens of companies who specialize in metal fabrication. The following in-depth workshops are being offered EXCLUSIVELY at METALCON 2025. and include content and instruction on metal fabrication.